重重压力之下,化工行业开始向压缩机要效益
【买空压机网】压缩机在化工行业可用于制冷和气体分离、合成气聚合、油的加氢精制、气体输送等。随着我国石油化工行业的快速发展,压缩机在石油化工生产中的应用变得越来越广泛。但是大部分化工企业压缩机的采购、运行管理都以稳定性、可靠性为先,能效考虑较少。加之工艺用压缩机种类繁多,型式各异,大部分功率大,难以监测,缺乏能效考核标准,导致我国化工行业大量压缩机低效运行。
近年来,随着《环境保护法》实施,重点行业设备节能监管越来越严、越来越细,越来越多的化工企业开始把压缩机的能效提升问题提上日程。
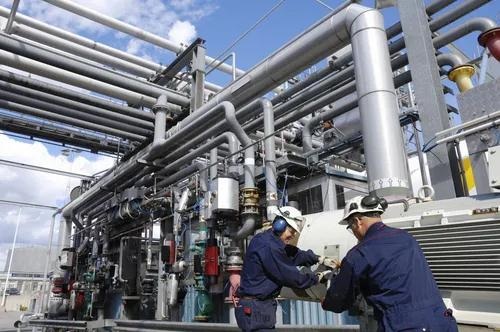
晋煤恒盛六改七提产能
2021年1月份,江苏晋煤恒盛化工股份有限公司氮肥二厂氨醇总产量达35002吨(表氨),刷新了该公司生产的最高纪录。
“压缩机成功六机改七机后,氨醇月度产量增加了3500吨以上,销售收入增加近1000万元,这标志着我们优化压缩机运行取得了巨大成功。”在罐区氨醇装车现场,恒盛化工销售公司经理邓振兴奋地说。
2019年,国内氮肥行情每况愈下,恒盛化工“18-30”氨氮系统被迫维持六机生产。特别是氮肥二厂单醇系统的全面停车,导致全公司生产总量和销售收入大幅下降,生产经营形势异常严峻。为了尽快摆脱当前的困难局面,最大限度发挥“18-30”系统的生产潜力,唯有提高装置效率和规模效益,以此降低成本,增加经济效益。
为此,氮肥二厂管理技术人员群策群力,积极动脑筋想办法,集思广益,并借助外部同行的有益经验和做法,对装置满负荷七机运行的设想进行了可行性评估。通过多次组织召开生产、管理、技术、财务,供应、销售等部门参与的综合论证,并从工艺、设备、安全环保等各方面进行了反复探讨,最终确立了七机运行的可行性。
七机运行试验,团队先后消除了多个瓶颈,重点实现了4个方面的重大突破:一是造气炉在无备用的情况下,保证了气量,突破了工艺关;二是造气炉在无备用情况下,突破了设备关;三是半水煤气脱硫塔的脱硫效率及阻力关顺利通过;四是煤气机无备用下的设备关。
同时,团队也打掉了一个个“拦路虎”。净化车间克服了变换气脱硫塔的阻力偏大的问题,保证了脱硫效率,并克服了脱碳系统吸附剂长期使用老化影响脱碳效果及装置能力不足的问题。合成车间压缩机克服了无备用机的现状,想方设法加强对压缩机的日常维护保养,提高检修质量和效率,延长运行周期,力保七机运行,解决了影响开七机的最大影响因素。氨合成岗位优化操作,悉心管理,顺利通过七机,合成氨日产量由原来的850吨左右提升到940吨左右。
开七机后,用电负荷增幅不少,2号主变压器容量不够,这样更需要热电车间加强锅炉、发电机的稳定运行,力争多发电,以保证七机的供电需要。为此,热电车间针对1号、3号锅炉运行周期长未进行彻底大修、故障频繁、影响锅炉稳定运行多的现状,想方设法提高维修质量,延长运行周期。
2019年9月5日,压缩机由六机改为七机运行试验正式实施,并取得一次试车成功,标志着全流程顺利通过,试验达产达标,且实现了安全环保稳产高产低耗稳定运行。由此实现了“18-30”系统运行质量效益效率的双提升,有效扭转了公司生产经营的被动局面。
延安石化技改节支显成效
近日,延安石油化工厂联合三车间通过对柴油加氢精制装置压缩机气量调节方法进行改良优化,改造后机组负荷大幅降低,电流由69A降低至49A,降幅约30%,每天节约电费约3540元。全年按运行8000小时计算,每年可节约电费约118万元。展现出连续、经济、高效、快捷、精确调节的效果。
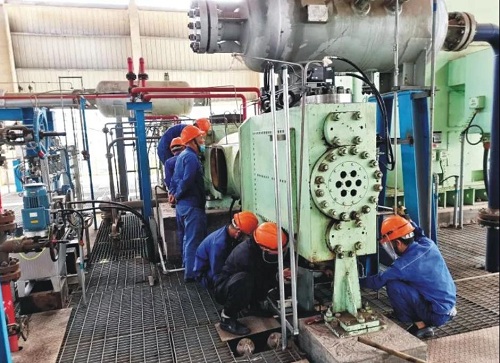
该厂柴油精制加氢装置新氢压缩机机组流量调节原设计为旁通阀回流调节,进气阀只有50%、100%两挡调节,大量工艺气循环回流,造成机组出力率降低,能耗增大,且影响装置平稳运行。同时,当压缩机处于满负荷状态下运行时,节能效果不明显、经济性较差。为此,该厂决定对压缩机调节方法进行改良升级。
该厂在大检修期间,针对柴油精制加氢装置新氢压缩机组织开展技术攻关,与设计院、制造厂家、同行业单位多次交流,最终确定压缩机气量调节方式由定量调节改为无级调节系统,通过HydroCOM气量无级调节系统连续调节压缩级进气阀开度,做到精准调节,精确匹配工艺生产所需气量,最大限度节约能源,实现气量0%-100%连续调节,轻松实现压缩机平稳启动、切换和停机。“该系统技术先进且成熟,可以实现压缩机的平稳启动、加载、切换和停机。”该车间副主任李杰介绍,在使用中,HydroCOM系统可通过压缩所需要的气量,最大限度的节约能源;通过智能化的液压调节机构,能够快速、精准地控制压力和流量,最终实现气量理论上“无级”调节。
“一次性的改造投入,换来的是压缩机‘终生’实现节电的成效。”李杰说,“无级”调节系统可将原内操频繁调整操作的工作省去,在优化操作的同时降低操作工的劳动强度和难度。
湖北化肥巧用压缩机降消耗
2020年,中国石化湖北化肥公司煤气化部坚持价值引领效益导向,持续推进百日攻坚创效行动,投用反吹气压缩机提高下游负荷,降低蒸汽消耗,持续优化空分装置产品结构,推动挖潜增效工作落实落地。1至3月,下游合成氨产量同比增加28.6%,运行部物耗能耗大幅降低。
煤气化装置是湖北化肥生产系统负荷提升的龙头,于2006年竣工投产,为下游装置提供原料合成气。煤气化部打破上下游管理围墙,开展技术攻关,成功投用反吹气压缩机,通过粗合成气替代氮气进行反吹,降低粗合成气中氮气含量,提高气化炉负荷降低消耗的同时,为下游高负荷生产提供保障。反吹气压缩机投用后,下游合成氨装置每小时产量突破46吨,日产量提高2.8%以上,实现增产增收的目标。目前,该运行部对反吹气压缩机开展特护工作,加大巡检频次,消除“跑冒滴漏”事不过夜;针对冷却水供应流程工艺变更,制订事故预案,落实防范措施,并下发到4个化工班组学习,定期开展事故演练,为装置长满优保驾护航。
咬定低压氮压机等大机组蒸汽消耗不放松,做好节能文章。结合公司单产合成氨的生产模式,运行部技术人员提出减少低压氮气用量,降低低压氮压机蒸汽消耗的思路。他们细化风险识别、落实防范措施,反复摸索尝试,经过二次降压操作,在保持公司低压氮气系统平衡,机组瓦温、推力、轴位移等在正常范围内波动的前提下,将0.7兆帕低压氮气管网优化降压至0.55兆帕,低压氮压机每小时蒸汽消耗从19.32吨降至17.95吨,消耗降低7%。下一步,运行部自我加压,将持续卡边操作,力争低压氮压机每小时蒸汽消耗降至17吨以下。
以上为正文!
买空压机网部分新闻素材来源于各大品牌公众号和压缩机网(www.compressor.cn).
压缩机网作为行业内最早的平台型网站.一直为空压机行业的发展而努力.
在此致以敬意. 希望有机会能一起合作.为用户提供最优质的行业资讯.